- 5 Ways Hybrid Design Delivers What Districts Need
- 1. Lower Costs
- 2. Faster Delivery
- 3. Less Disruption
- 4. Great Predictability
- 5. More Flexibility
- Hybrid Success Stories
- 1. Case Study 1: Isaac L. Sowers Middle School
- 2. Case Study 2: Flora Arca Mata Elementary School
- 3. Case Study 3: Lemon Grove Early Childhood Education Center
- The Value of Collaborative Partnerships
How Hybrid Design Maximizes Flexibility and Value for School Districts
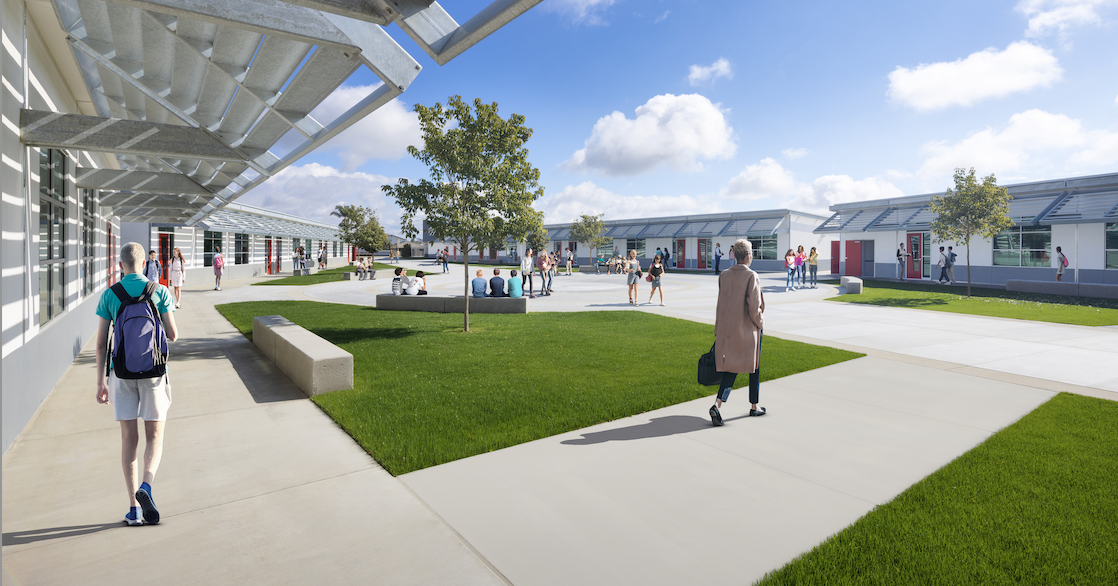
Hybrid design is an important tool in facilities planning, leveraging the benefits of both modular and conventional construction methods to deliver innovative buildings quickly, affordably and sustainably. Three successful hybrid projects provide a roadmap.
School districts know they need to modernize facilities—what they don’t always know is how to do it quickly and affordably to meet a list of demands that grows longer every year.
The solution? Hybrid design—a fast-growing concept that blends traditional and modular buildings to meet individual site and programming needs. Instead of downsizing space or downscaling specs to reconcile rising costs and shrinking budgets, a hybrid plan combines construction methods on a single campus—sometimes within a single building—to meet high expectations with fewer resources.
It’s a creative option for districts that lack the funds, or time, for all stick-built construction, but don’t want to compromise their vision—a situation many California school districts are facing.
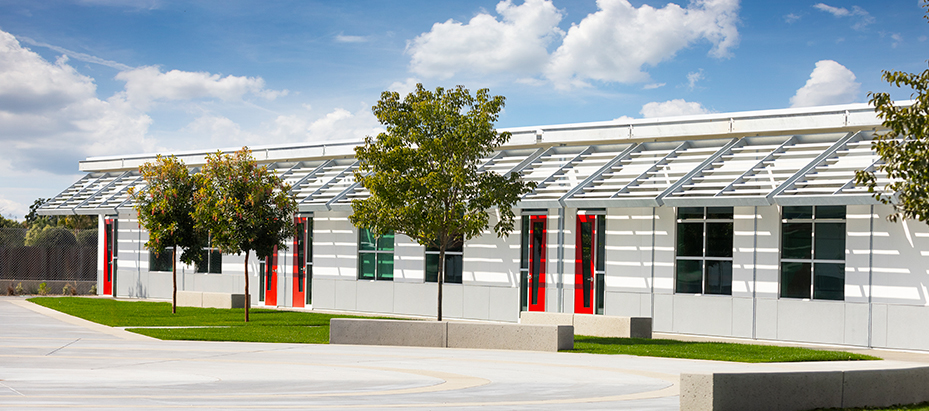
5 Ways Hybrid Design Delivers What Districts Need
Today’s students need healthy, high-quality space that supports 21st century learning. They need it now… and budget-strapped school districts are tasked with providing it.
Hybrid design is a proven, solution-driven approach that has allowed dozens of California school districts to expedite their modernization and expansion plans with modular construction. A hybrid plan uses modular advantages to layer in efficiencies at every phase of design and production, leveraging advanced modular building technologies and methods to benefit districts in five pivotal ways.
Lower Costs
Construction is costly, and traditional buildings are, by far, the most expensive to construct. Material waste and work stoppages due to adverse weather or labor shortages drive costs upward, leading to budget overruns.
Adding modular to the mix optimizes project efficiencies, reducing construction costs by 25-35% without compromising quality or performance. A streamlined modular process and automated construction pay back quickly, lowering upfront costs and providing ongoing savings throughout the building lifecycle.
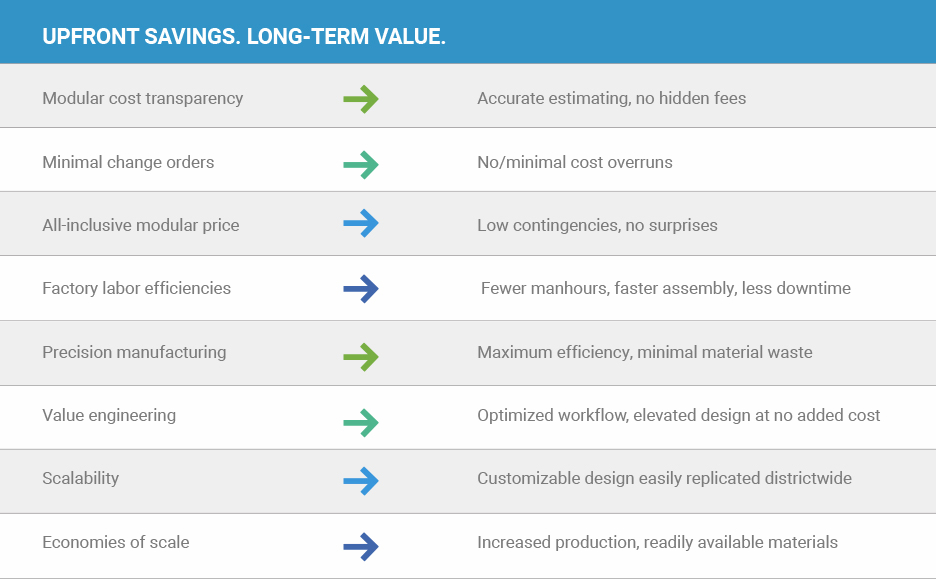
Faster Delivery
Traditional buildings are constructed entirely onsite—a linear process that delays the start of construction until the sitework and building foundations are completed.
Hybrid design cuts construction time in half by fabricating modular buildings offsite in the factory while simultaneously building traditional structures onsite. It’s a practical solution that allows districts to meet time-critical needs and execute modernization plans up to 60% faster—even for large, complex projects.
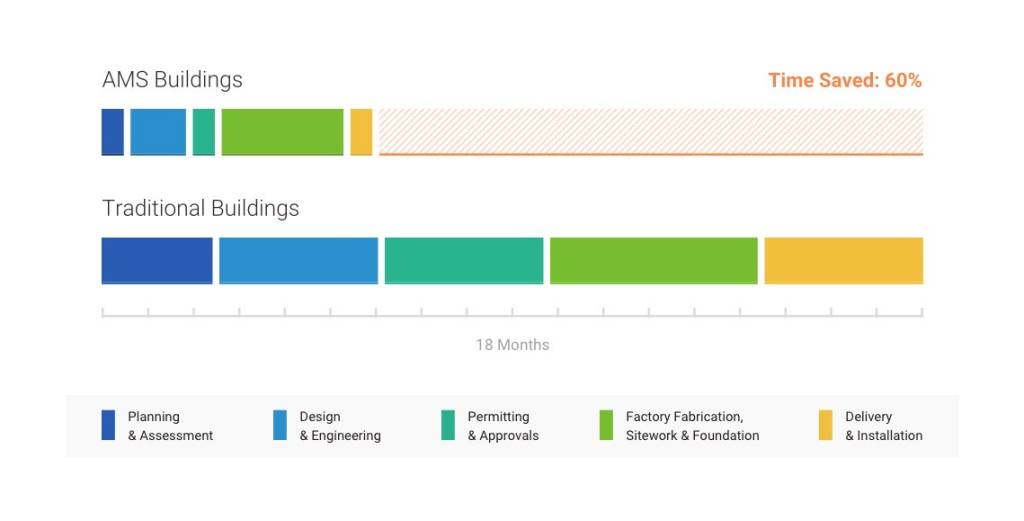
Less Disruption
Onsite construction creates noise, dust and mess on a school campus. Even with safety procedures in place, heavy machinery and increased traffic pose a risk for students and disrupt a school’s schedule—an inconvenience that can go on for years. Air and noise pollution spread beyond the school to negatively impact neighbors, the community and the environment.
Moving construction offsite to the factory significantly reduces both the amount and duration of disruption to daily activities. Building modules are fabricated and stored at the factory until sitework is complete, then delivered 90-95% complete and installed, finished and connected to onsite utilities within days. Less time onsite means less inconvenience, less risk and a more sustainable building.

Great Predictability
Conventional construction has many uncontrollable variables. Adding contingencies to the budget attempts to account for uncertainties like inclement weather, an unstable labor market, material spoilage and human error, but a standard contingency tacks an extra 5-10% onto the project cost.
Modular construction isn’t impacted by weather or fluctuations in the local labor supply. Automating production in a climate-controlled environment reduces errors and delays to near-zero, ensuring reliable on-time, on-budget, to-spec delivery year-round, with minimal need for contingencies. Predictive scheduling allows districts to pre-schedule modular deliveries during school breaks to avoid disruption.
More Flexibility
While today’s modular buildings are highly efficient, they’re equally sophisticated, designed to look, feel and perform like traditional buildings. Virtually any conventional design can be modularized to capture a client’s unique vision, using advanced technology to deliver a finished building that’s virtually indistinguishable from a traditional structure.
Districts have the flexibility to create fully-custom pre-engineered (PE) designs or customize DSA Pre-Check (PC) designs for accelerated delivery. The ability to replicate exterior colors and finishes and add custom architectural details either onsite or offsite, can unify modular and traditional buildings to create a cohesive hybrid aesthetic on new or established campuses.
Hybrid Success Stories
Successful hybrid design balances customization and cost, finding the optimal mix of modular to stick-built and configuring buildings to meet classroom and specialty needs at the best cost. It’s a site-specific solution that addresses unique problems and priorities in line with the project budget and schedule.
Here’s a look at three successful new builds that overcame challenges to achieve project goals in very different ways.
Case Study 1: Isaac L. Sowers Middle School
Case Study 2: Flora Arca Mata Elementary School
Case Study 3: Lemon Grove Early Childhood Education Center
Case Study 1: Isaac L. Sowers Middle School
PARTNERS: Huntington Beach City School District and Studio W Architects
SIZE: 62,200 SF total/30,000 SF modular
COST: $54 million (est)
COMPLETION: January 2024 (Phase I)
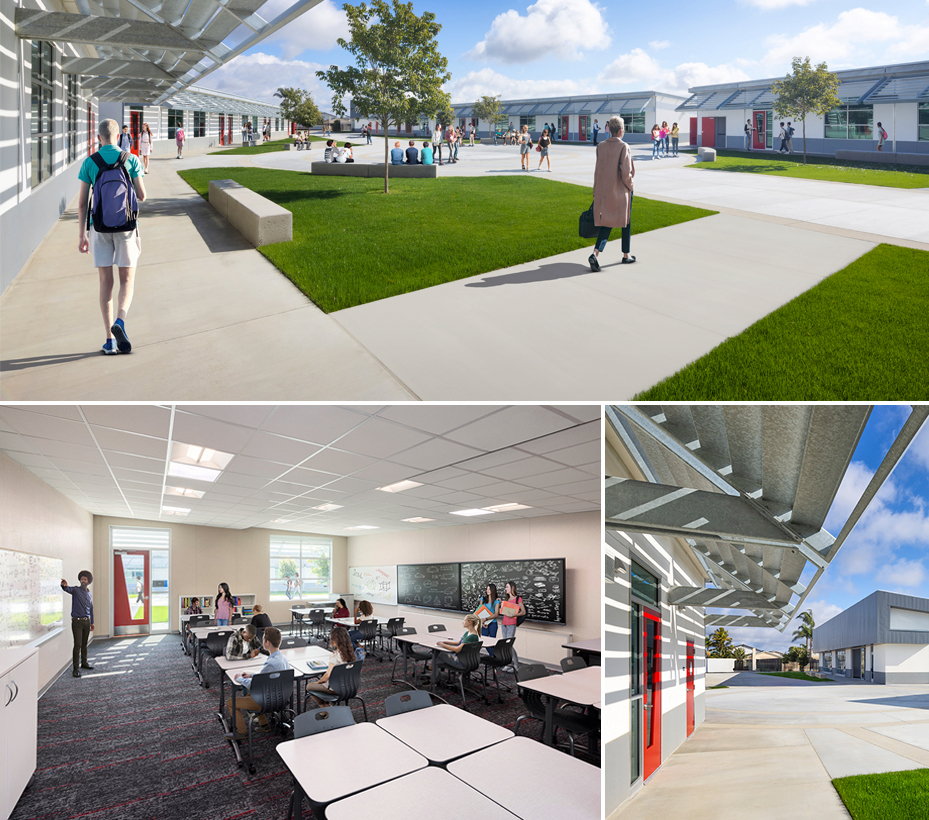
The Problem: The Sowers Middle School campus was vintage 1970s, ill-equipped to support the 21st century programming the Huntington Beach City School District (HBCSD) was committed to providing. The portable classrooms were outdated and energy-inefficient, the infrastructure was not conducive to collaborative learning and the campus layout did not allocate exterior space for outdoor learning and social activities.
The Process: HBCSD’s Facilities Master Plan called for Sowers’ entire campus to be modernized using Measure Q bond funds. After assessing the school’s needs and site issues, Studio W Architects, the Architect-of-Record, presented HBCSD with two options:
- Modernize the existing campus or
- Rebuild the campus with new construction
HBCSD and Studio W concluded that new construction would be more cost-effective and developed a conventional plan to revitalize the entire campus, replacing the dated portables and “honeycomb” design with energy-efficient new buildings designed for 21st century learning.
Challenges: The conventional concept captured the district’s vision, but when it came time to build, the $72.2 million price tag exceeded the district’s funds. With construction costs escalating and site issues adding to the expense, the design team needed to find a more economical solution.
Hybrid Design: Instead of scaling back the plan, Studio W proposed a hybrid design, incorporating AMS modular classroom buildings to lower costs while meeting the project team’s high expectations. AMS replaced Sowers’ old portables with five new GEN7 high-performance buildings customized to Sowers’ specs and arranged to enclose a large central quad. Building fronts open to the shared quad for indoor/outdoor learning while rear elevations form a secure perimeter that heighten student safety.
A stick-built administration building, student union, gym, locker room facility and STEM lab complete the revitalized campus, integrating seamlessly with the modular buildings to provide a cohesive aesthetic.
Outcome: The hybrid design reimagines the campus for next-gen learning with collaborative spaces, art and science labs and open classrooms that take advantage of the SoCal weather. GEN7’s DSA-PC design lowered upfront and lifecycle costs with energy-efficient features that promote productive learning—abundant natural light, whisper-quiet acoustics and natural ventilation systems that ensure healthy IAQ.
Going with a 60/40 mix of modular and stick-built reduced the cost of the large-scale project to around $54 million, executing HBCSD’s plan at a savings of $130/SF vs conventional construction.
Case Study 2: Flora Arca Mata Elementary School
PARTNERS: Stockton Unified School District and TETER Architects + Engineers
SIZE: 58,686 SF total/46,752 SF modular
COST: $38.2 million
COMPLETION: August 2020
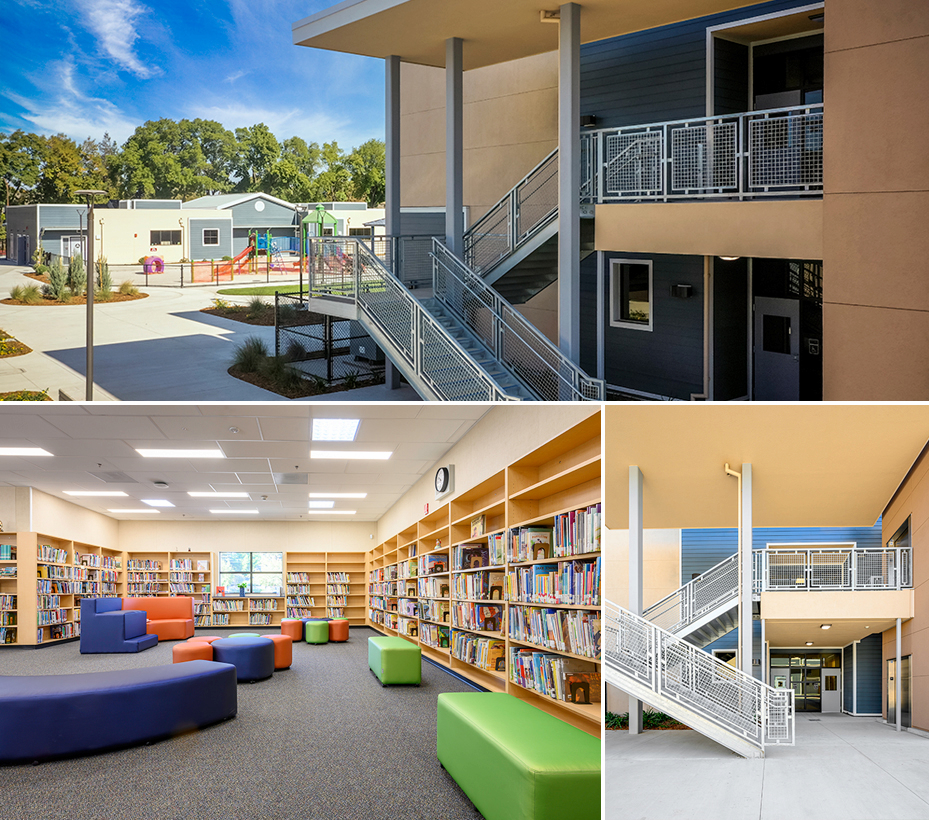
The Problem: SUSD was experiencing capacity constraints. After years of transporting students in the Quail Lakes neighborhood to other schools, the district approved plans for a new K-8 school that could accommodate 500 students. SUSD’s goal was aggressive—to design and build a new facility within two years, meeting current programming requirements with the flexibility to adapt to future needs.
The Process: Faced with a tight budget and an even tighter timeline, SUSD and AOR TETER Architects took a practical approach. They turned to modular construction from the outset, partnering with AMS to design and build a complete modular campus on SUSD land.
Challenges: The high-profile project—named to honor beloved local education pioneer Flora Arca Mata—needed to be fully customized to meet the community’s high expectations and the strict requirements of the Quail Lakes HOA. SUSD challenged the design team to deliver the community’s exact vision on an accelerated schedule, creating a campus that looked stick-built on a modular budget.
Hybrid Design: A hybrid plan aligned costs and aesthetics, mixing two AMS EVOLVE modular classroom buildings and an admin/library building with a site-built multipurpose building to complete a fully-custom campus built to the same design standards as a conventionally-built campus.
AMS pushed the envelope on design, elevating features and materials to deliver the buildings quickly without sacrificing the aesthetic the team wanted to achieve. High-end materials were customized to create a distinctive identity for the new school. Blue lap siding, white fascia and trim, privacy windows and traditional gable roofs create a residential look that’s carried across modular and traditional buildings to blend the new school into its upscale neighborhood.
Outcome: Constructing modular buildings in the AMS factory while the site contractor completed demolition, grading and foundations onsite cut the schedule in half. The highly-efficient modular construction process lowered upfront costs, with AMS value-engineering the design to save even more. Using enclosed, conditioned hallways in the two-story modular classroom building and arranging admin building modules to maximize the utility of every square foot saved thousands of dollars.
Flora Arca Mata used less than 1% contingency. Minimal change orders and no overtime—due to AMS’ precision manufacturing—kept the project on-schedule and allowed SUSD to re-allocate reserve funds for add-on improvements. The hybrid solution—an 80/20 mix of modular to stick-built—was responsive to needs, meeting all project goals while saving SUSD $10 million in costs and accelerating delivery of a complete custom campus by a year.
Case Study 3: Lemon Grove Early Childhood Education Center
PARTNERS: Lemon Grove School District and PBK Architects
SIZE: SF total/40,000 SF modular
COST: $38 million
COMPLETION: Fall 2024-Spring 2025 (est.)

The Problem: The 2021-2022 Education Budget Bill requires all California public schools to offer Universal TK by the 2025-2026 school year. Like many districts, Lemon Grove did not have the infrastructure to expand or add transitional kindergarten (TK) programming on its existing elementary school campuses.
The Process: The state’s stringent TK requirements—a minimum 1,350 SF with in-classroom restroom—made it unfeasible to convert existing space to TK. LGSD quickly identified new construction as the best approach, with modular construction the most expedient, cost-effective solution. Partnering with AMS jumpstarted design, providing access to DSA-approved TK designs that could be customized to LGSD’s vision and budget.
The Challenges: With land and space at a premium in urban San Diego County, building new facilities on all LGSD campuses would be difficult. The district and community wanted the new facilities to be progressive and amenity-rich, capable of meeting a variety of early learning needs—an expensive undertaking, even with the ability to scale custom DSA-PC designs districtwide.
Hybrid Design: The design team took an innovative approach, electing to centralize TK expansion for all LGSD schools in a consolidated Early Childhood Education Center at the Palm Campus. Creating one large PreK-TK learning complex maximized the district’s flexibility while containing costs to provide an inclusive space that promotes the socio-emotional growth and development of all Lemon Grove 2-4-year-olds.
The GEN7 modular classroom buildings are the core of the new campus, creating a series of student “neighborhoods” clustered around a winding walkway that connects a variety of outdoor recreational and independent learning spaces. A large multipurpose building is stick-built, meeting student and staff needs with a library, central multipurpose room and administrative offices.
The new campus is sustainable and connected to nature, with solar panels, wellness gardens and native-landscaped paths that encourage children to explore, discover and learn in creative ways.
Status: Modular’s parallel construction process is critical to accelerating project delivery. The project broke ground in fall 2023, with sitework and construction of the traditional MPR building taking place onsite while 16 modular classroom modules are being fabricated in the AMS factory. The classrooms will be delivered 95% complete in spring/summer 2024, with the new facility on schedule to open later this year.
The Value of Collaborative Partnerships
Each of these success stories has a critical element in common: a strong partnership with a commitment to bringing a shared vision to life. Successful projects take a team approach, bringing school districts, architects, educators and builders together to find the best solution to fulfill a project’s unique needs.
At AMS, we’re invested in your project’s success. We partner with all stakeholders, using our experience and insight to find creative solutions that lower costs, add value and expedite delivery. Our AMS team works with yours from project planning through delivery, helping you:
- Assess needs and define wants, needs and priorities
- Set clear goals and target outcomes
- Find the right building solution and customize it to your project needs, goals and budget
Every project is different, and so are our building solutions. AMS offers a full range of modular buildings, from fully-custom to turnkey, each configured to integrate seamlessly into a hybrid plan.
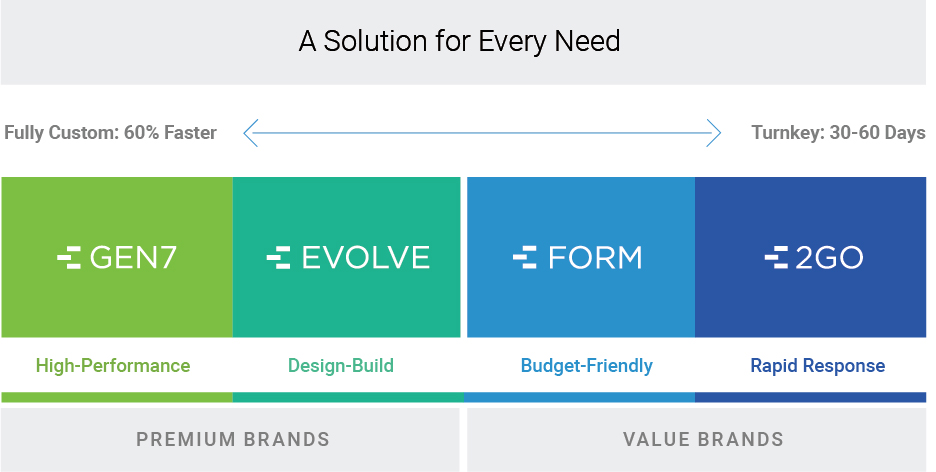
Modularize conventional designs to deliver one-of-a-kind buildings. Meet immediate needs with turnkey buildings that can be delivered in as little as 30-60 days. Or balance flexibility and cost with a semi-custom building upgraded to your project specs.
Hybrid design opens up new possibilities, giving you the flexibility to build the facilities you need with the funds you have available. Ready to build? We’re ready to help!
Partner with us and bring your vision to life.