5 Myths About Modular Construction — and Why You Shouldn’t Believe Them
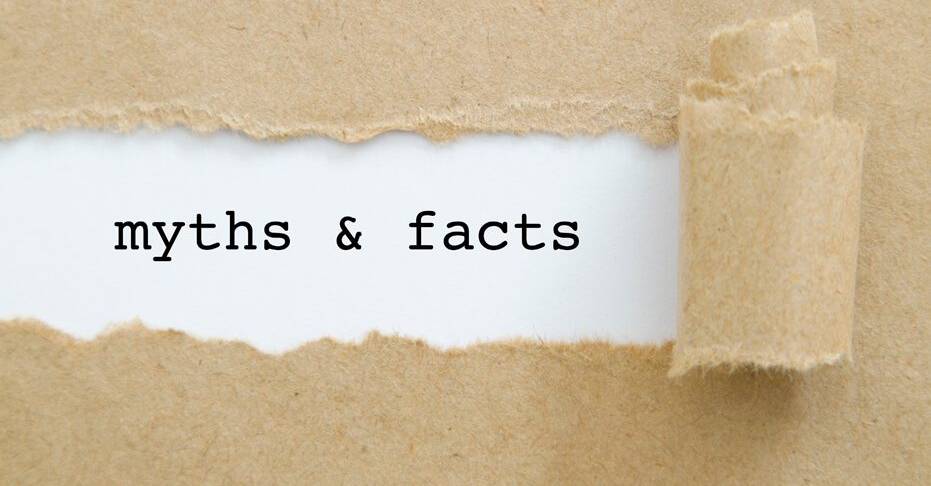
Modular has been around for decades—and so have the myths. To set the record straight, we’ll explore five popular beliefs about modular construction that just aren’t true—and one that is. Get the facts… and use them to find the best building solution for your project.
We’ve all heard them: popular truisms that are widely accepted as fact, despite evidence to the contrary.
Some are outdated, some are based on a lack of information and some are simply misleading, passed along without a sense of authenticity. They run the gamut from how modular buildings are built, how they perform and how they’re perceived to how they look and what value they deliver, now and over time.
Call them myths, misconceptions, stereotypes or clichés; they have one thing in common: they aren’t true. Undisputed, they lead to decisions based on faulty assumptions when the best decisions are based on facts, supported by evidence that proves what modular construction can offer and how modular buildings can benefit school districts looking to modernize.
Modular Construction: Myths vs. Facts
What’s true and what’s not? We’ll tell you, show you and give you the facts you need to make informed decisions for your projects.
Myth #1: “Modular is cheap.”
Some people still picture trailers or portable buildings from the 70s when they hear the word “modular.”
The truth is: Modular costs less, but it isn’t lower quality. Mobile buildings from the 20th century can’t compare with 21st century modular. Today’s modular buildings are constructed from the same, or superior, materials and offer the same features and amenities as traditional buildings. Every modular building goes through a stringent plan review and approval process and is third-party inspected to assure compliance to the same building codes and regulations as conventional construction.
In fact, modular standards are often higher and much more controllable. AMS designs and constructs buildings to meet standards that are more rigorous than the state of California requires. The cost savings come from economies of scale, minimal waste and the production efficiencies of automated assembly.
Building in a controlled factory environment, using state-of-the-art technology, produces a more reliable product and the best possible outcome: a higher quality building delivered at a lower cost.
See the Difference
Old school portable vs. high-end modular
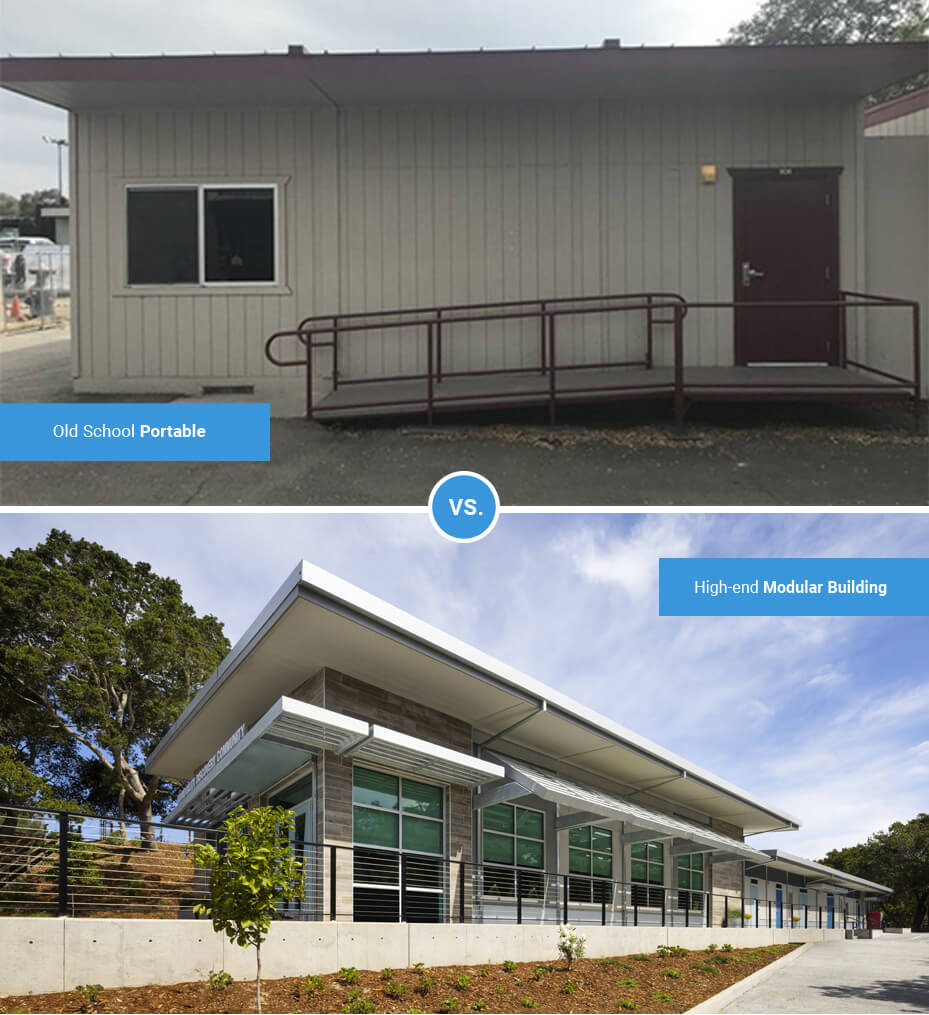
Myth #2: “Modular isn’t built to last.”
Old school thinking still lingers, and it goes like this: modular buildings are meant to be temporary, they’re not as safe, they don’t last as long.
The truth is: Premium modular buildings have the same 50-year lifecycle as stick-built structures. Materials and mechanical systems are carefully selected for high durability, and a precision construction process makes every building very safe, built to withstand extreme weather conditions and perform reliably over decades of use.
The all-steel moment frame of AMS and GEN7 modular buildings is structurally superior to wood framing and resists rot, mold and insect damage—common shortcomings of wood construction that can negatively impact occupant health and comfort. Metal windows and doors increase structural integrity, seldom need replacing or painting and are highly recyclable. Tough, dependable finishes, like concrete floors, stucco cladding and hardy plank exteriors, are stylish and sustainable with minimal upkeep.
Not only do modular buildings outlast many other buildings, they’re safer. more sustainable and lower maintenance, significantly reducing lifecycle costs to save schools money.
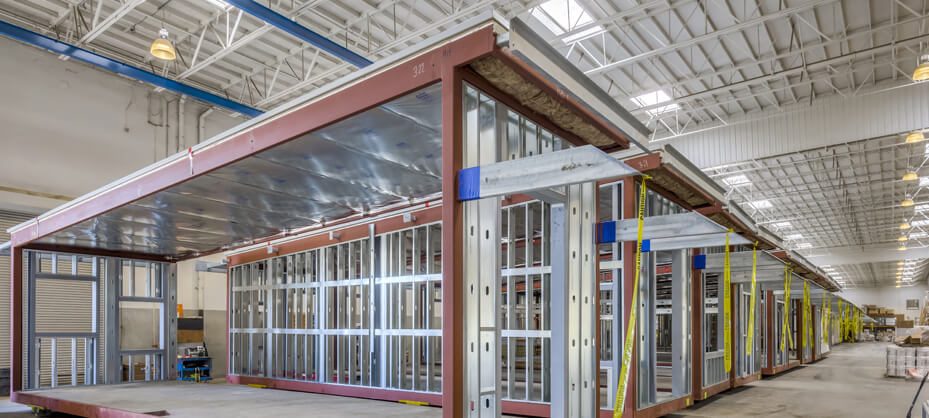
Myth #3: “Modular isn’t flexible enough.”
We hear it all the time: “With modular, you get what you get.”
The truth is: Modular buildings can be just as flexible as stick-built. Virtually any conventional design can be built in a factory using the modular process. AMS utilizes advanced technology to “modularize” a design, deconstructing it into the most efficient combination of modules to achieve a school’s exact specs. The modules are assembled on the production line and connected into a complete building onsite.
Different size and shape modules can be joined together into any size building, customized to any style, configured to any site. Modular buildings can be single-story, two-story, L-shaped or U-shaped, with clear spans and high ceilings, open access or enclosed for greater security—whatever a school needs. Finished buildings can include custom architectural details, integrate site-built elements and be customized to blend with existing buildings, creating a unique aesthetic that reflects a school’s identity.
Modular matches buildings to a school’s vision. You don’t “get what you get”—you get what you want.
See the Difference
Myth #4: “Architects don’t want to use modular.”
A common misperception is that architects push clients to use conventional designs instead of modular.
The truth is: About half of architects’ projects include modular. The reasons vary—it’s more budget-friendly, it’s faster, scheduling and quality are more reliable. Modular designs are adaptable, as freestanding buildings or combined with traditional buildings in a hybrid plan that offers the best of both worlds. Modular hybrid design is an important part of architects’ build strategies, and architectural firms appreciate its predictability in delivering complex projects on tight timelines and budgets.
Modular is far from a fallback or compromise—architects are now featuring modular in their initial plans. As modular technology and designs become increasingly sophisticated, modular is becoming an innovative go-to option, not Plan B when stick-built is too expensive.
Architects not only want to use modular; they recommend modular to their most discerning clients and feature it as a centerpiece of high-end designs—with proven success.
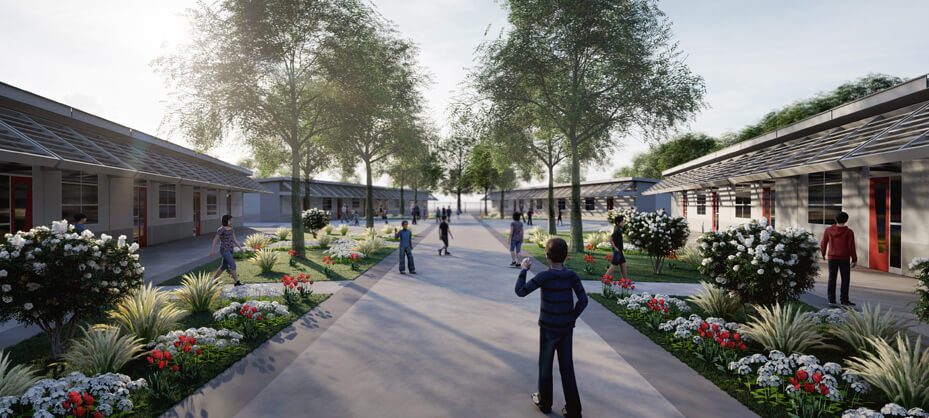
Myth #5: “You can tell it’s modular.”
Some people say modular buildings look “different” than traditional buildings.
The truth is: High-end modular buildings are virtually indistinguishable from stick-built—structurally, functionally and aesthetically. Modular designs can be fully customized inside and out to look, feel and perform exactly how the school wants them to look, feel and perform—just like traditional buildings.
AMS and GEN7 modular buildings can be equipped with the same features and finishes as conventional construction and configured to provide the same wide-open floorplans and high-tech infrastructure for modern collaborative learning. They can meet the same energy and sustainability goals and often exceed performance at a much lower cost. School districts who tour AMS and GEN7 buildings say they can’t see a visual or functional difference between modular buildings and traditional.
Here’s a four-building hybrid campus that mixes stick-built and modular. Can you tell what’s modular?
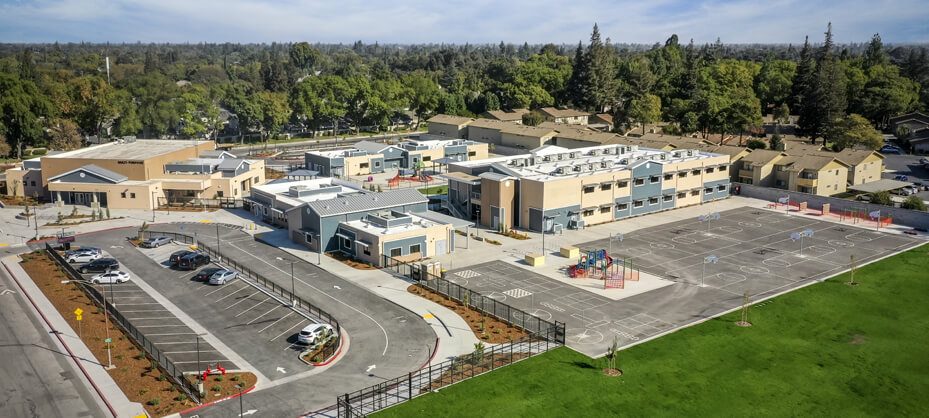
Here’s What Else Is True: Modular Is the Fastest Growing Construction Method
Modular construction is projected to grow more than 8% annually between 2022 and 2027—and potentially beyond.
Despite pandemic-driven cost increases and supply chain issues, modular construction is in a multi-year boom and for good reason: modular delivers high-quality buildings 60% faster than conventional construction at a cost 25-35% less.
Modular’s shorter schedules and get-more-for-less budgets allow school districts to modernize faster and more affordably than any other construction method, while delivering quality facilities customized to a school’s unique needs and programming.
That’s a difference schools like.
The Biggest Myth of All?
“Stick-built is a better solution for schools.”
The truth is: Different options give schools a choice. The best building solution is the one that best meets a school’s needs. Increasingly, schools are discovering that the best solution is modular—either as a standalone building or combined with stick-built in a custom hybrid design.
When you separate the myths from the facts, it’s easy to see why modular has become a proven go-to delivery method for California schools.
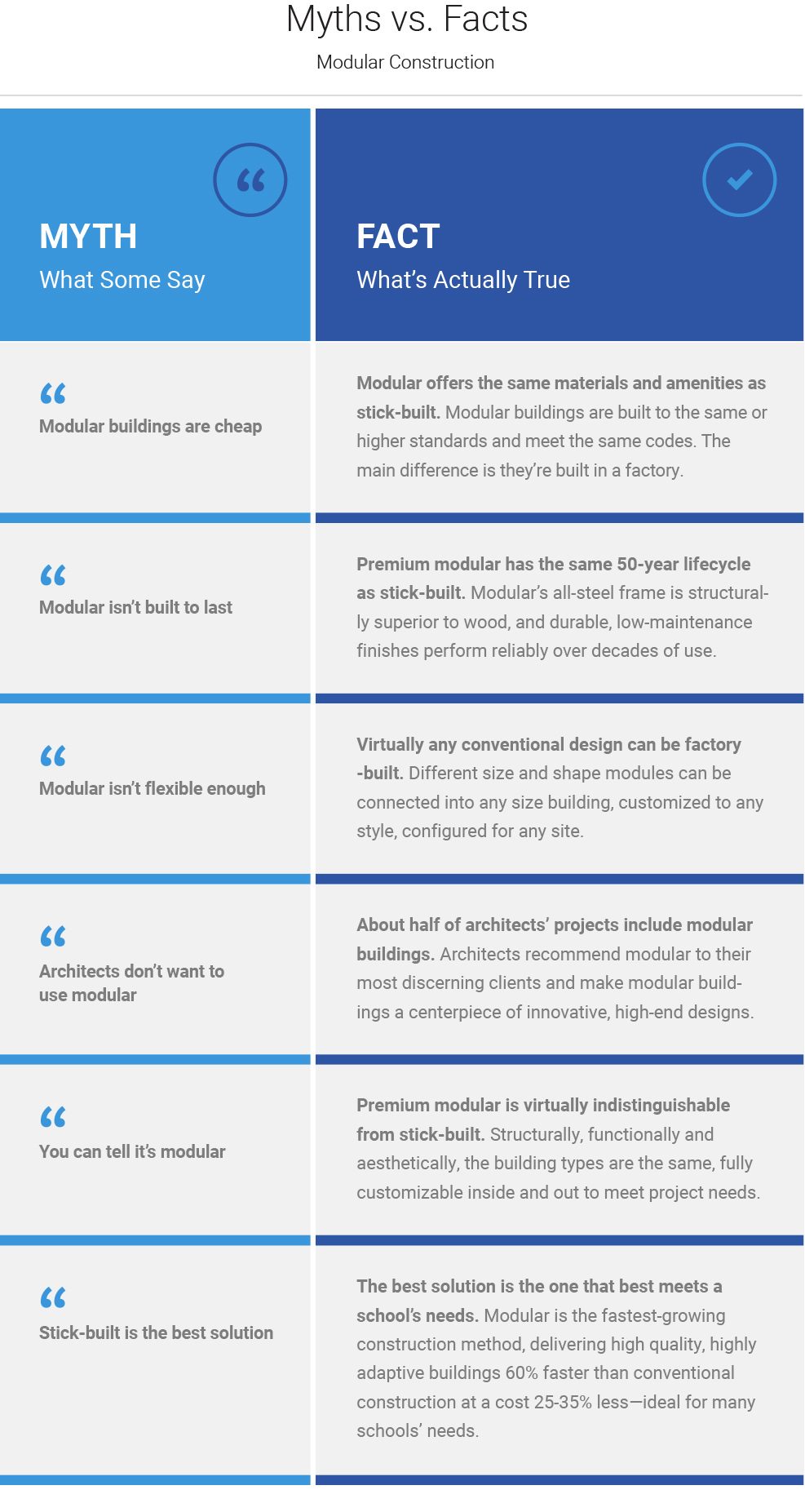
Let AMS help you find the right building solution for your project.
See the difference our premium modular buildings can make.
Ready to build? Request a Quote.